3D-Drucker führt Silikone und Hochleistungskunststoffe zusammen
- Pressemitteilungen
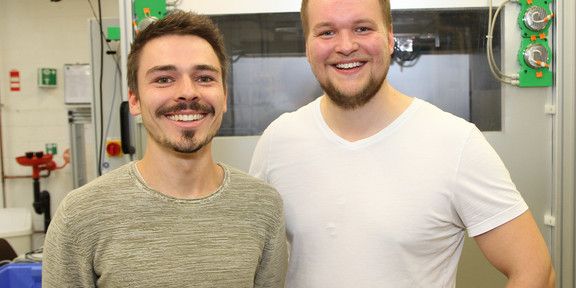
Der 3D-Multiprint-Drucker steht noch unverkleidet in der Werkstatt der Fakultät Maschinenbau am Campus Nord: Ein Würfel mit einer Kantenlänge von knapp zwei Metern. Zuleitungen, Reihen von Schrauben, Warnhinweis vor Strahlung: Das Druckermodell zeugt von viel Handarbeit und ist ein Unikat. „Wir haben ihn weitestgehend selbst erstellt“, sagt Jasper Gruson. „Selbst die Druckköpfe sind Eigenentwicklungen“.
Im weltweit boomenden Markt von 3D-Druckern ist dieses Gerät ein Einzelstück. Der Drucker soll komplexe Hybridprodukte produzieren. Konkret soll er Gegenstände in einem Arbeitsgang aus unterschiedlichen Standard- und Hochleistungsthermoplasten, aber auch Hochleistungskunststoffen und Silikonen in einem einzigen unterbrechungsfreien Produktionsprozess erzeugen. „Eine konkrete Anwendung ist beispielsweise eine Prothese“, berichtet Philipp Kemper. „Wenn ein Mensch auf solch ein Hilfsmittel angewiesen ist, erfordert dies eine individuelle Anpassung.“ Das gilt besonders für den Übergang der Gliedmaße des Menschen zur Prothese: Dieser Übergang muss hautfreundlich und exakt passend angefertigt werden. Dafür werden flexible Silikonpolster passgenau in die Prothese integriert. Diese Kunststoff-Silikon-Verbindung ist wegen der unterschiedlichen Materialeigenschaften herausfordernd.
Der Drucker, den Gruson und Kemper entwickeln, ermöglicht das. Gleichzeitig wird die Fertigung hochautomatisiert, ressourcenschonend und somit zeitsparend und kostengünstig. Der erste Zielmarkt ist die Sanitäts- und Orthopädiebranche mit der Herstellung von Komponenten für individuelle Hilfsmittel wie Prothesen. Den Anwendungsmöglichkeiten sind aber kaum Grenzen gesetzt – bis hin zu Sitzen für Formel-1-Piloten.
Das neuartige 3D-Drucksystem wollen Gruson, Kemper und der Softwareentwickler Frithjof Pollmüller auf der Basis eines bestehenden Labormusters, also eines 3D-Spezialdruckers, entwickeln. Der wurde im Zuge des Projekts „FilChange – Flexible-3D-Printing“ des EFRE-Förderprogramms „START-UP-Hochschul-Ausgründungen NRW“ gebaut und in Betrieb genommen. Grundlage für die Technik ist ein neu entwickeltes Filament-Verarbeitungsmodul, das die TU Dortmund zum europäischen Patent angemeldet hat.
Das Entwicklerteam geht bei seiner Arbeit – Projektstart war am 1. März dieses Jahres – in mehreren Schritten vor: Zunächst optimieren sie den 3D-Spezialdrucker für die Verarbeitung von Hochleistungskunststoffen. Gleichzeitig entwickeln sie ein neuartiges Silikonverarbeitungsmodul. Im nächsten Schritt schaffen sie – erstmals im 3D-Druck – eine Verarbeitungsmöglichkeit für Hochleistungsthermoplaste und Silikone in einem Produkt. Mithilfe einer neuen Softwarelösung sollen die einzelnen Materialien belastungsgerecht und zeiteffizient miteinander verbunden werden.
Mit dem Förderprogramm EXIST-Forschungstransfer unterstützt das Bundesministerium für Wirtschaft und Energie herausragende forschungsbasierte Gründungsvorhaben wie MedTech-Multiprint. Das Team wird auf dem Weg in die Selbständigkeit vom Centrum für Entrepreneurship & Transfer (CET) der TU Dortmund begleitet. „3D-Druck ist eine Schlüsseltechnologie der Zukunft“, sagt Albrecht Ehlers, Kanzler der TU Dortmund und CET-Vorstand. „Ich freue mich, dass wir dem Start-up den Weg von der Forschung in die Selbstständigkeit ebnen können. Das ist ein schöner Erfolg unseres Centrums für Entrepreneurship & Transfer.“